читайте также
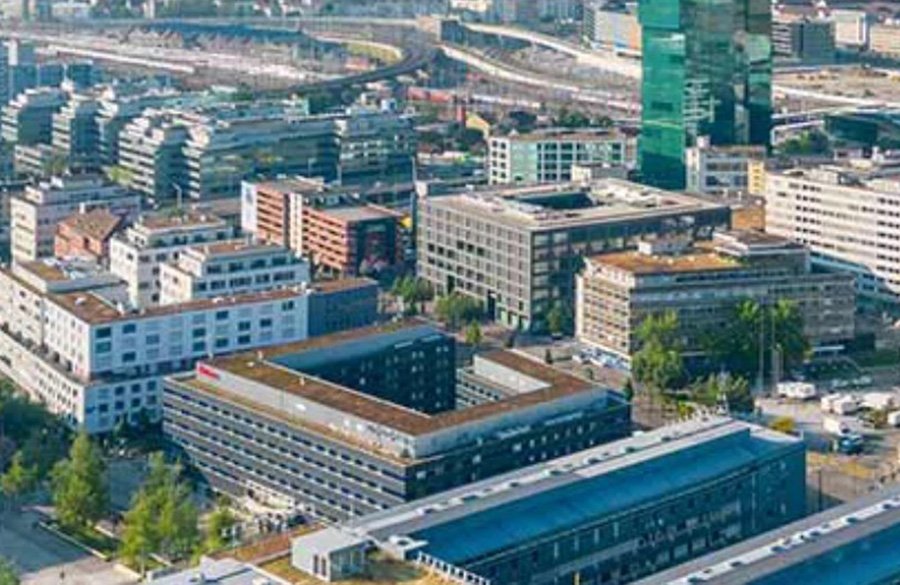
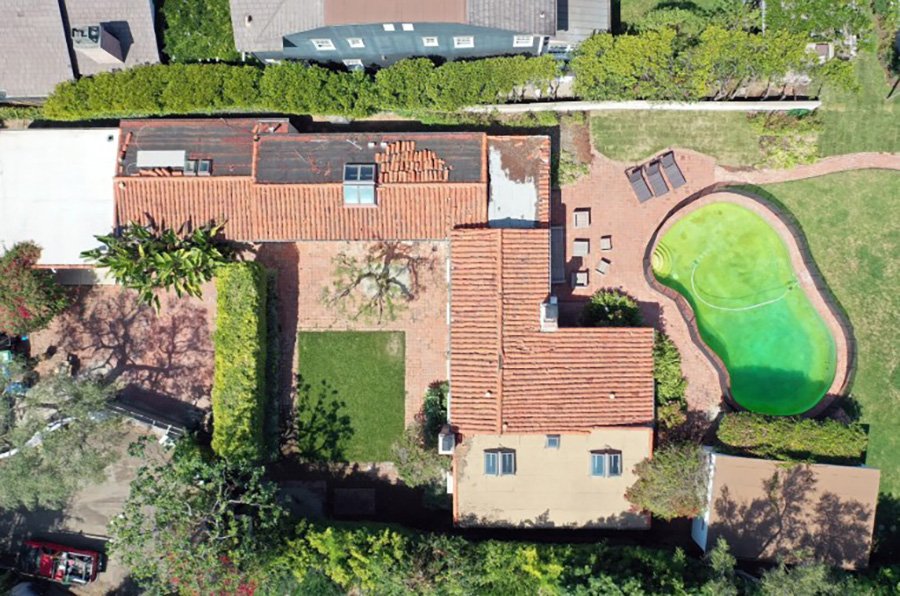
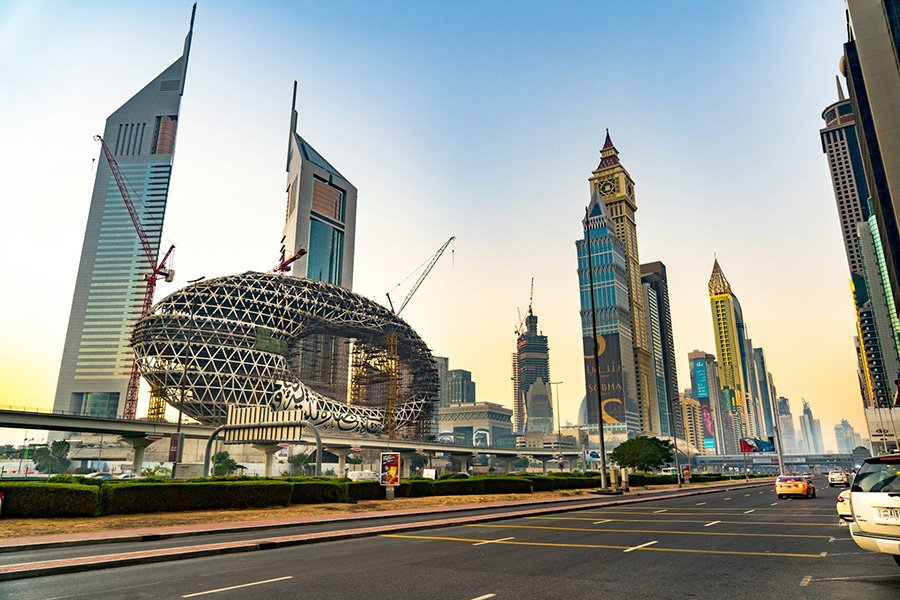
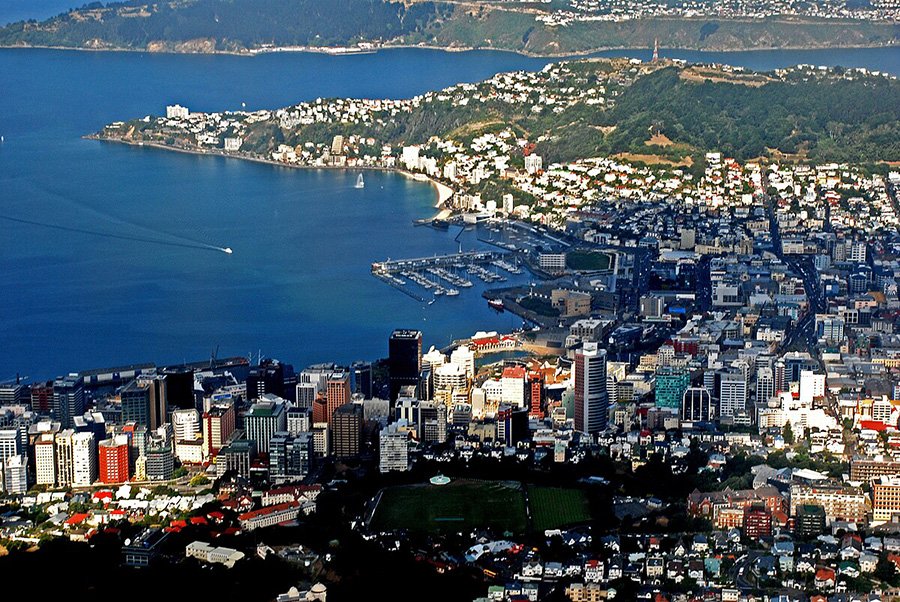
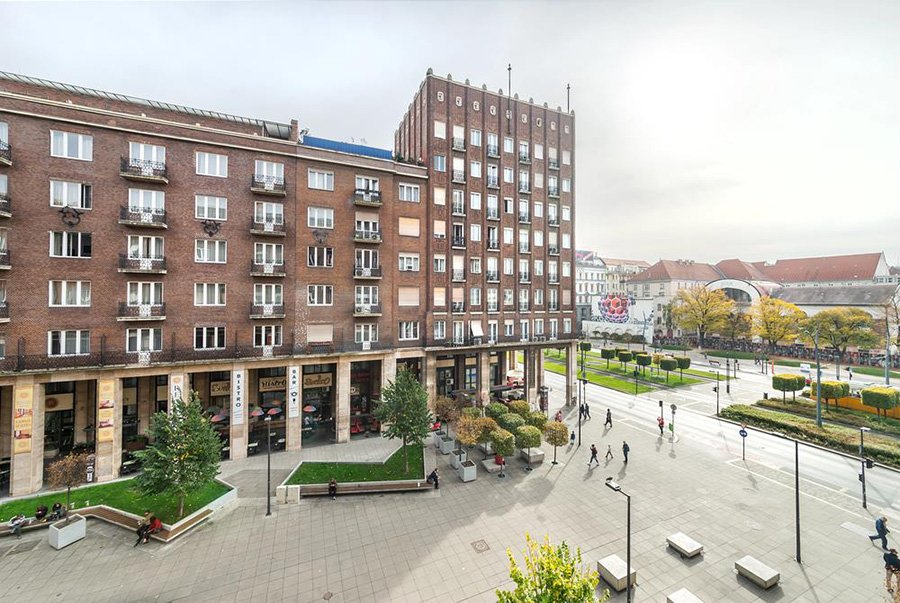
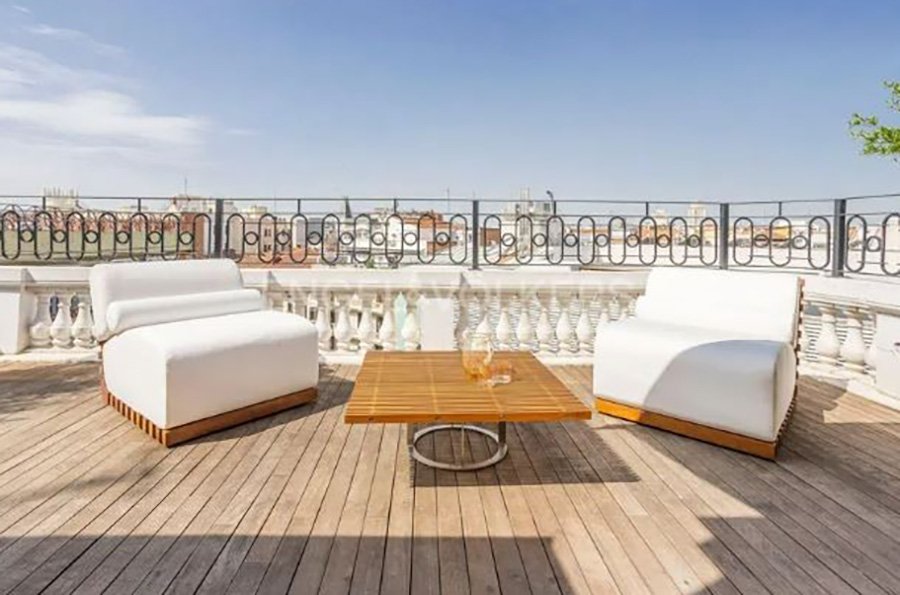
Вusiness / Investments / Analytics / Reviews / News / Real Estate / USA / Real Estate USA 20.05.2025
U.S. Warehouses and Trump Tariffs: How Bonded Warehouses Are Saving Businesses
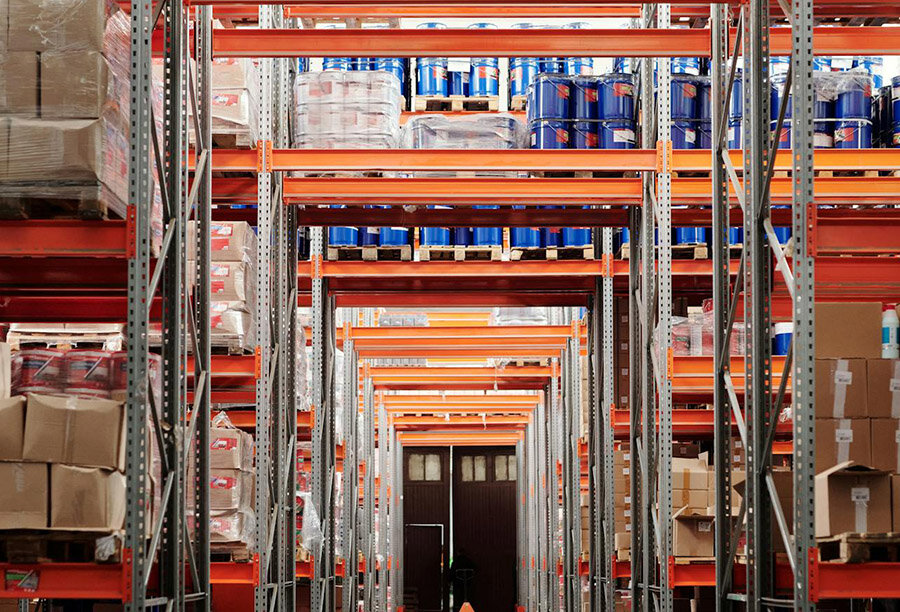
In 2025, bonded warehouses in the United States have become a vital lifeline for importers caught in the crossfire of Donald Trump’s aggressive tariff agenda. As Bloomberg reports, demand for these facilities has surged following the imposition of steep tariffs on imports from dozens of countries, including China.
Bonded warehouses allow goods to be stored for up to five years without paying customs duties. This offers critical flexibility: importers can wait out trade policy shifts or release products to market in small batches, stretching out tariff payments over time. In a period of trade uncertainty, this option has become increasingly attractive.
According to John Shea, head of Momentum Commerce, which supports Amazon-based brands, bonded warehouses are not a way to “game the system” but rather a means to buy time amid shifting demand, margins, and regulations. “Tariffs have become a moving target,” he explains.
At Flexe—a startup network that connects around 1,000 warehouse owners—demand for bonded storage has jumped sixfold. One client, who sells over $100 million worth of Christmas trees annually, used a bonded facility to delay tariff payments until peak season. Flexe co-founder Karl Siebrecht noted that bonded warehouse space is now 60% more expensive than standard industrial property.
In Bayonne, New Jersey, Accem Warehouse leased all 220,000 square feet of its facility even before ships arrived, anticipating a tariff-driven rush. “The phones were ringing off the hook,” recalls company president Jerry Mecca. While some deals were canceled during a temporary 90-day reprieve, owners expect renewed demand from Chinese clients, where tariffs remain in place.
According to Flexe’s estimates, only about 21 million square feet of U.S. warehouse space is bonded—a narrow slice of the market. But surging demand could change that. More operators are exploring federal certification, though this requires security investments and up to a year of processing time. “There will be a short-term shortage,” warns Brandon Young of Seller Systems, “but supply will likely catch up.”
Some companies got ahead of the curve. Afar Logistics in Tacoma, Washington, completed certification in 2024. “Perfect timing,” says CEO Davit Habte. His 37,000-square-foot facility can be fully occupied by a single client.
According to the National Customs Brokers & Forwarders Association, demand is highest in coastal hubs like Los Angeles and Long Beach—gateways for up to 40% of Chinese imports. Gene Seroka, executive director of the Port of Los Angeles, noted that these ports are the first to feel the impact of tariff policy shifts.
Robert Krieger, president of Krieger Worldwide, sees bonded warehouse demand as a sign of deeper supply chain restructuring. One client is seeking space for 40 containers of South Asian apparel, hoping to use a temporary duty-free window. Another is considering exporting pre-imported goods to third countries like Canada to avoid U.S. tariffs altogether.
Thus, bonded warehouses have become an essential crisis logistics tool—helping companies stay resilient amid unpredictable trade policy swings. Scarcity, rising costs, and complex regulations are reshaping the industrial real estate market. In this volatile climate, bonded facilities serve as temporary buffers, allowing businesses to adapt to shifting rules of the game.
According to The Wall Street Journal, container shipments from China to the U.S. have fallen by a third, putting more strain on domestic warehouses and increasing bonded facility demand. Bisnow reports that bonded warehouses are now part of broader strategies that also include Foreign Trade Zones (FTZs), which allow goods to enter without duties until they reach the domestic market—giving companies more supply chain flexibility.
Flexport notes that many major retailers are pairing bonded warehouses with manufacturing relocation—from China to Vietnam or Mexico—to cut costs and reduce exposure to tariff risks. Meanwhile, The Guardian highlights the domestic labor consequences: rising logistics costs and tariff instability could lead to job losses among warehouse and transport workers, especially smaller operators.